In the realm of Good Manufacturing Practices (GMP) factories, particularly those within the pharmaceutical industry, maintaining a sterile and controlled environment is paramount.
This is where the cleanroom airlock emerges as an essential element, playing a critical role in safeguarding the integrity of these sensitive spaces.
I. Unveiling the Cleanroom Airlock
1. What is Cleanroom Airlock
According to the World Health Organization's (WHO) GMP guidelines, a cleanroom airlock is an enclosed space typically equipped with two or more doors. These doors are strategically positioned between different rooms (e.g., cleanrooms with varying cleanliness levels) or areas. The primary function of the airlock is to regulate airflow between these connected spaces, minimizing the risk of contamination. Importantly, airlocks can be specifically designed for personnel or material transfer.
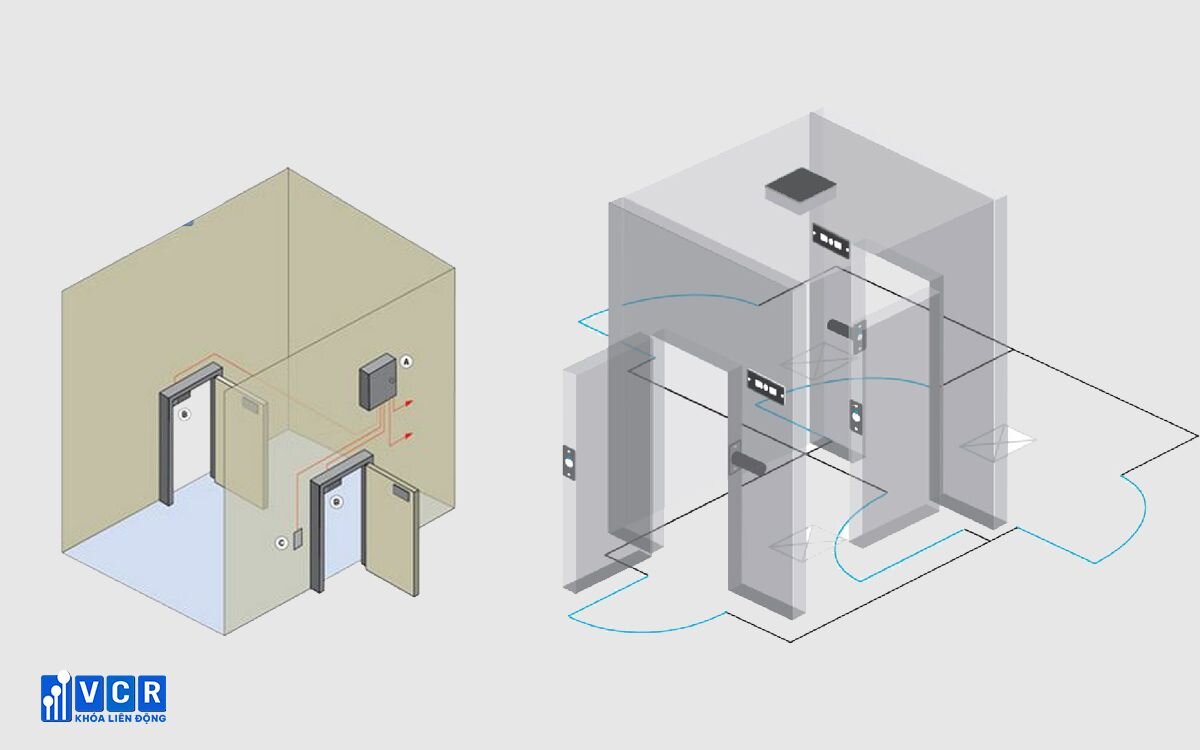
See more: Airlocks and Access control
2. Additional Functions
Beyond airflow control, cleanroom airlocks often serve as buffer rooms. Here, materials undergo sterilization procedures before being permitted to enter the cleanroom, further bolstering contamination prevention efforts.
II. The Necessity of Airlocks in Cleanrooms
1. Preventing Cross-Contamination
The fundamental purpose of utilizing airlock systems within cleanrooms lies in preventing cross-contamination. This refers to the unintended transfer of contaminants, such as microbes or particulate matter, from one cleanroom area to another. By creating a physical barrier and regulating airflow, airlocks effectively minimize the likelihood of such occurrences, safeguarding the integrity of the controlled environment.
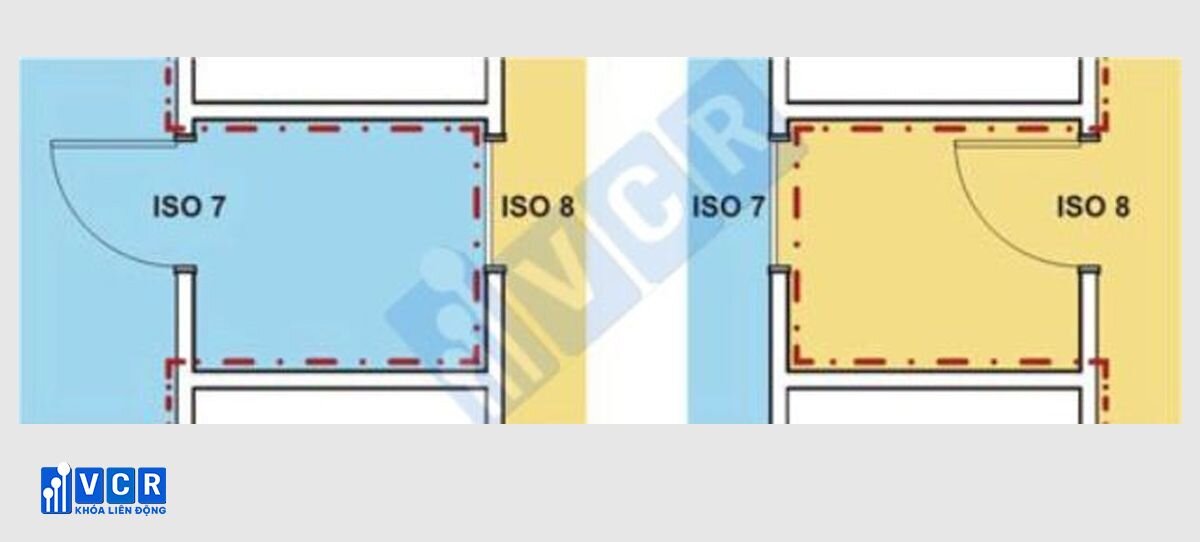
See more: Buffer room and its applications in clean room
2. Maintaining Pressure Differentials
Cleanroom airlocks are meticulously designed to maintain a differential pressure between the cleanroom environment and adjoining areas. This pressure difference, typically established by the HVAC system, is crucial. It creates a directional airflow, preventing unfiltered air from entering the cleanroom and potentially compromising its sterility. As per WHO GMP, a differential pressure of 10-15 pascals is considered the standard within these environments. It is crucial to note that achieving a higher pressure difference necessitates a more complex and consequently, costlier system.
Cleanroom Airlock Construction
Airlocks in cleanroom environments serve as critical access points, and their construction must carefully consider factors like durability, hygiene, and contamination control.
Material of Cleanroom Airlock
The choice of materials for airlock construction hinges on individual facility requirements and budget considerations. Common options include:
- Cleanroom panels: These prefabricated panels offer rapid installation and a seamless integration with existing cleanroom walls. They are often constructed from materials like galvanized steel or aluminum with a painted or laminated finish.
- Electrostatically painted steel: This option provides a cost-effective solution while maintaining durability and cleanability. The electrostatic painting process ensures a uniform and adherent finish, minimizing the risk of particle shedding.
- Stainless steel (inox): For applications demanding superior corrosion resistance and aseptic conditions, stainless steel stands out as the optimal choice. Its impervious surface minimizes harboring of contaminants and facilitates thorough cleaning and disinfection practices.
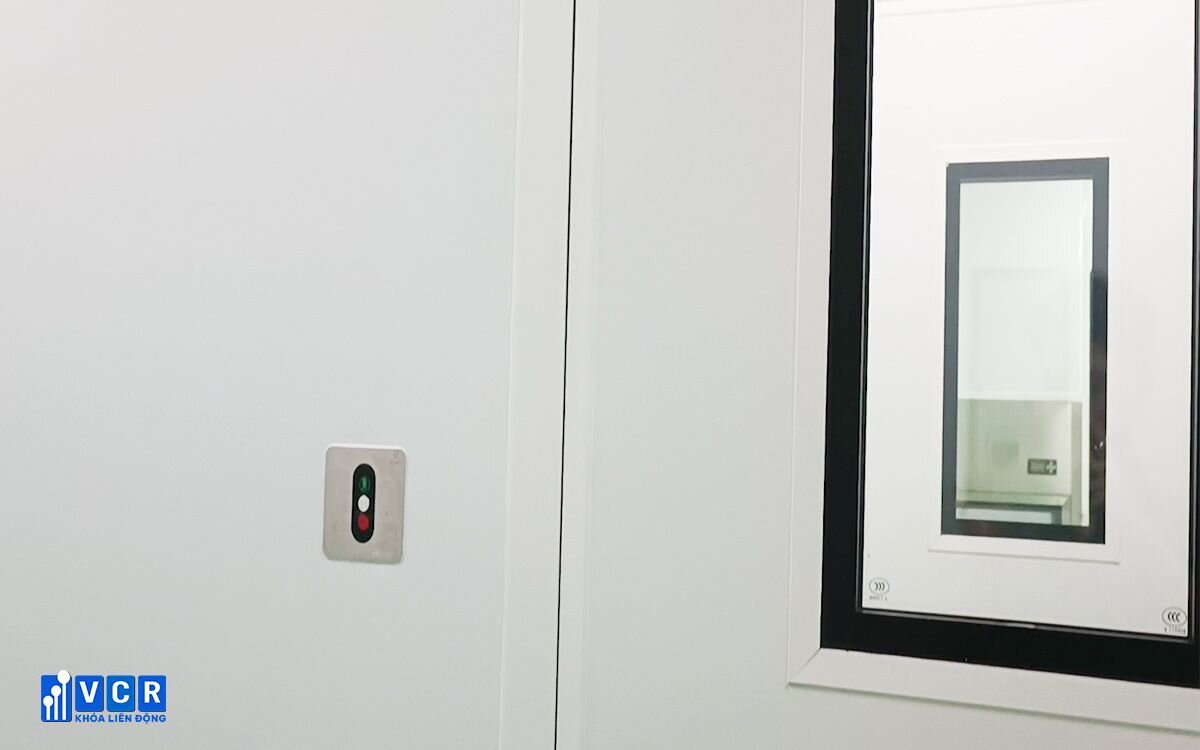
See more: Why Cleanrooms Depend on Door Interlock Systems
Ensuring Controlled Access
Every airlock typically incorporates two doors equipped with an interlock system. This mechanism guarantees that only one door can be opened at a time, effectively preventing cross-contamination between adjacent cleanroom areas.
Conclusion
Cleanroom airlocks serve as invaluable safeguards within GMP facilities, particularly those in the pharmaceutical industry. By controlling airflow, preventing cross-contamination, and maintaining necessary pressure differentials, they play a pivotal role in ensuring the sterility and integrity of these critical cleanroom environments.